反矩陣算法的問題,我們搜遍了碩博士論文和台灣出版的書籍,推薦李金洪寫的 全格局使用PyTorch - 深度學習和圖神經網路 - 基礎篇 和DavidC.Howell的 基礎行為科學統計學都 可以從中找到所需的評價。
另外網站資訊科技研究- 求反矩陣(Inverse Matrix)也說明:矩陣運算 · 同質系統(Homogeneous System) · 求反矩陣(Inverse Matrix) · 2x2 反矩陣 ... 求反矩陣(Inverse Matrix). 2x2 反矩陣公式. GNU-R: P <- array(0, dim=c(4,4)) P[1 ...
這兩本書分別來自深智數位 和雙葉書廊所出版 。
嶺東科技大學 資訊科技系碩士班 張安成所指導 李佳昇的 雙基地雷達系統於過載目標下到達方向與離開方向之聯合估測 (2021),提出反矩陣算法關鍵因素是什麼,來自於雙基地雷達、過載、到達方向、離開方向、雜訊子空間、奇異值分解、特徵值分解。
而第二篇論文朝陽科技大學 工業工程與管理系 林宏達所指導 鄭丞凱的 電腦視覺技術應用於手工具組裝之零件瑕疵檢驗 (2021),提出因為有 自動化檢驗、手工具組裝、瑕疵檢驗、R-CNN網路模式的重點而找出了 反矩陣算法的解答。
最後網站6.1 線性方程組與行列式運算則補充:一是消去部份將矩陣A 利用列運算求得上三角矩陣. 二是反代(Backward Substitution)部份來求得所要的答案. 吾人假設一方程組如下所示:. 10. 5. 3. 2. 3. 2. 1. = +. + x x.
全格局使用PyTorch - 深度學習和圖神經網路 - 基礎篇
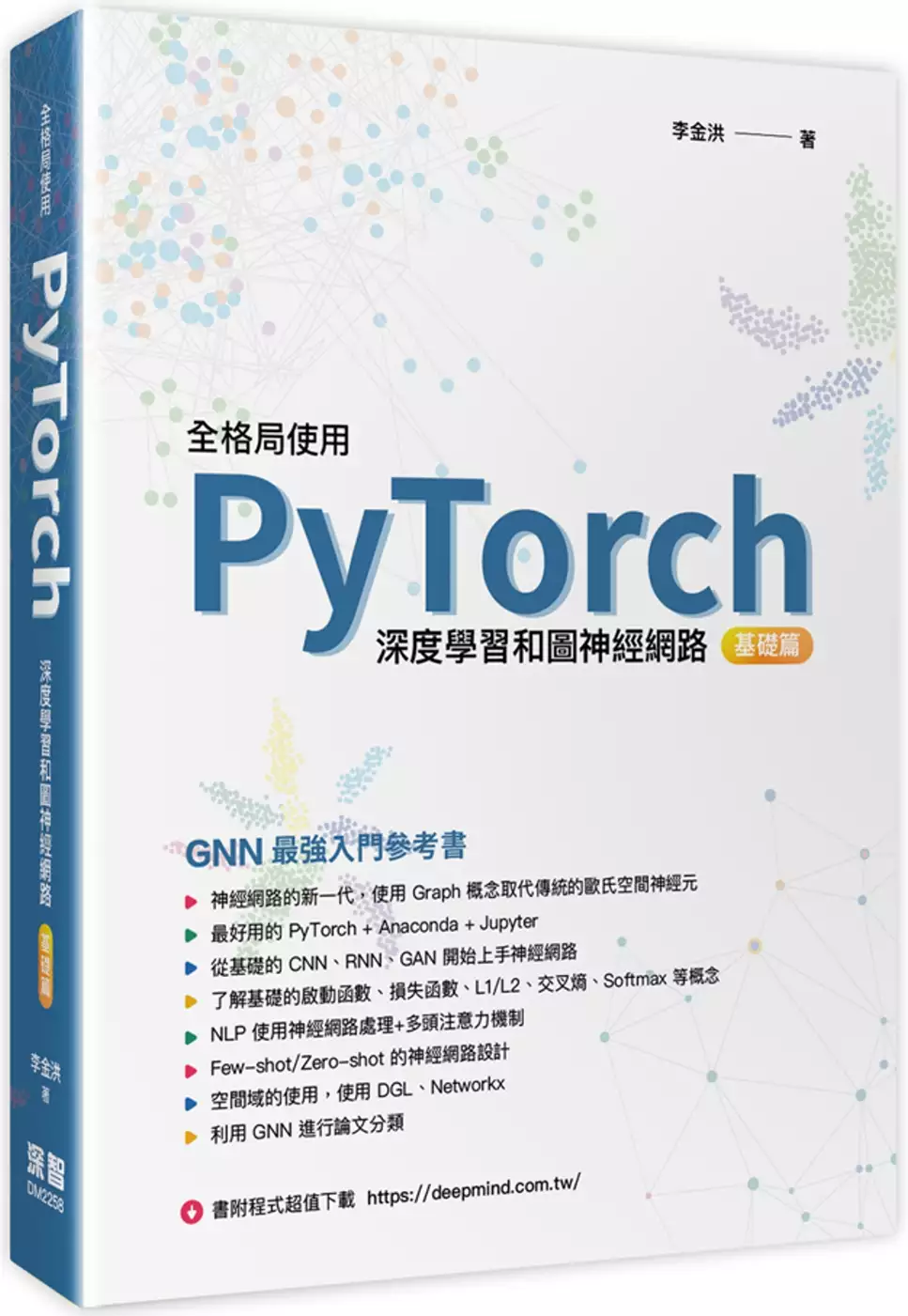
為了解決反矩陣算法 的問題,作者李金洪 這樣論述:
深度學習擅長處理結構規則的多維資料(歐氏空間),但現實生活中,很多不規則的資料如:社群、電子商務、交通領域,多是之間的關聯資料。彼此間以龐大的節點基礎與複雜的互動關係形成了特有的圖結構(或稱拓撲結構資料),這些資料稱為「非歐氏空間資料」,並不適合用深度學習的模型去分析。 圖神經網路(Graph Neural Networks, GNN)是為了處理結構不規則資料而產生的,主要利用圖結構的資料,透過機器學習的方法進行擬合、預測等。 〇 在結構化場景中,GNN 被廣泛應用在社群網站、推薦系統、物理系統、化學分子預測、知識圖譜等領域。 〇 在非結構化領域,GNN 可以用在圖
型和文字等領域。 〇 在其他領域,還有圖生成模型和使用 GNN 來解決組合最佳化問題的場景。 市面上充滿 NN 的書,但卻沒有一本完整說明 GNN,倘若不快點學這個新一代的神經網路,你會用的普通神經網路馬上就會落伍了!非歐氏空間才是最貼近人類生活的世界,而要真正掌握非歐氏空間的問題解決,GNN 是你一定要學的技術,就由本書一步步帶領你完全攻略! 〇 使用 Graph 概念取代傳統的歐氏空間神經元 〇 最好用的 PyTorch + Anaconda + Jupyter 〇 從基礎的 CNN、RNN、GAN 開始上手神經網路 〇 了解基礎的啟動函數、損失函數、L1/
L2、交叉熵、Softmax 等概念 〇 NLP 使用神經網路處理 + 多頭注意力機制 〇 Few-shot/Zero-shot 的神經網路設計 〇 空間域的使用,使用 DGL、Networkx 〇 利用 GNN 進行論文分類 本書特色 ~GNN 最強入門參考書~ ● 以初學者角度從零開始講解,消除讀者學習過程跳躍感 ● 理論和程式結合,便於讀者學以致用 ● 知識系統,逐層遞進 ● 內容貼近技術趨勢 ● 圖文結合,化繁為簡 ● 在基礎原理之上,注重通用規律
雙基地雷達系統於過載目標下到達方向與離開方向之聯合估測
為了解決反矩陣算法 的問題,作者李佳昇 這樣論述:
本論文係於雙基地雷達系統中處理過載目標時之聯合到達方向(direction of arrival, DOA)和離開方向(direction of departure, DOD)估測問題,過載目標係指雙基地雷達系統所欲偵測目標的數目大於發射機元件和接收機元件的乘積的數目。考慮某一雙基地雷達系統,其發射與接收陣列分別由具備M個與N個元件之均勻線性天線陣列所組成,而發展被偵測目標的數目大於 的估測演算法,在期望於低計算複雜度與高目標物容量的情況下,於接收端以提升角度估測之解析度,並且針對要提升處理目標數目必須增加系統有效自由度伴隨而來的計算負荷,發展低計算複雜度的技術進行探討,為了達成有效估測的目
的,本論文包含二個主要課題,第一個課題為雙基地雷達系統於過載目標下到達方向與離開方向之聯合估測,基於自相關矩陣重新表示法的處理方式係利用目標反射波訊號的子空間特徵和基於陣列響應的Khatri-Rao (KR)乘積之相關性,所提出的聯合DOA和DOD估測器具有處理目標數目遠大於發射機元件和接收機元件數目乘積的能力和導致解析極限的顯著改善。第二個課題則於傳送端加入一個編碼雷達訊號之基於空間時間雙基地雷達架構,於接收端發展一種角度估測方法以提升角度估測之解析度,並增加目標物估測數目之容量。同時為了降低計算複雜度,故本論文亦將於第一和二個課題中分別發展相對之具有計算效率的雜訊子空間投影矩陣估測技術,來
降低高維度奇異值分解(singular value decomposition, SVD)和特徵值分解(eigen value decomposition, EVD)的計算負荷。最後經由電腦模擬驗證所提出方法的有效性。
基礎行為科學統計學
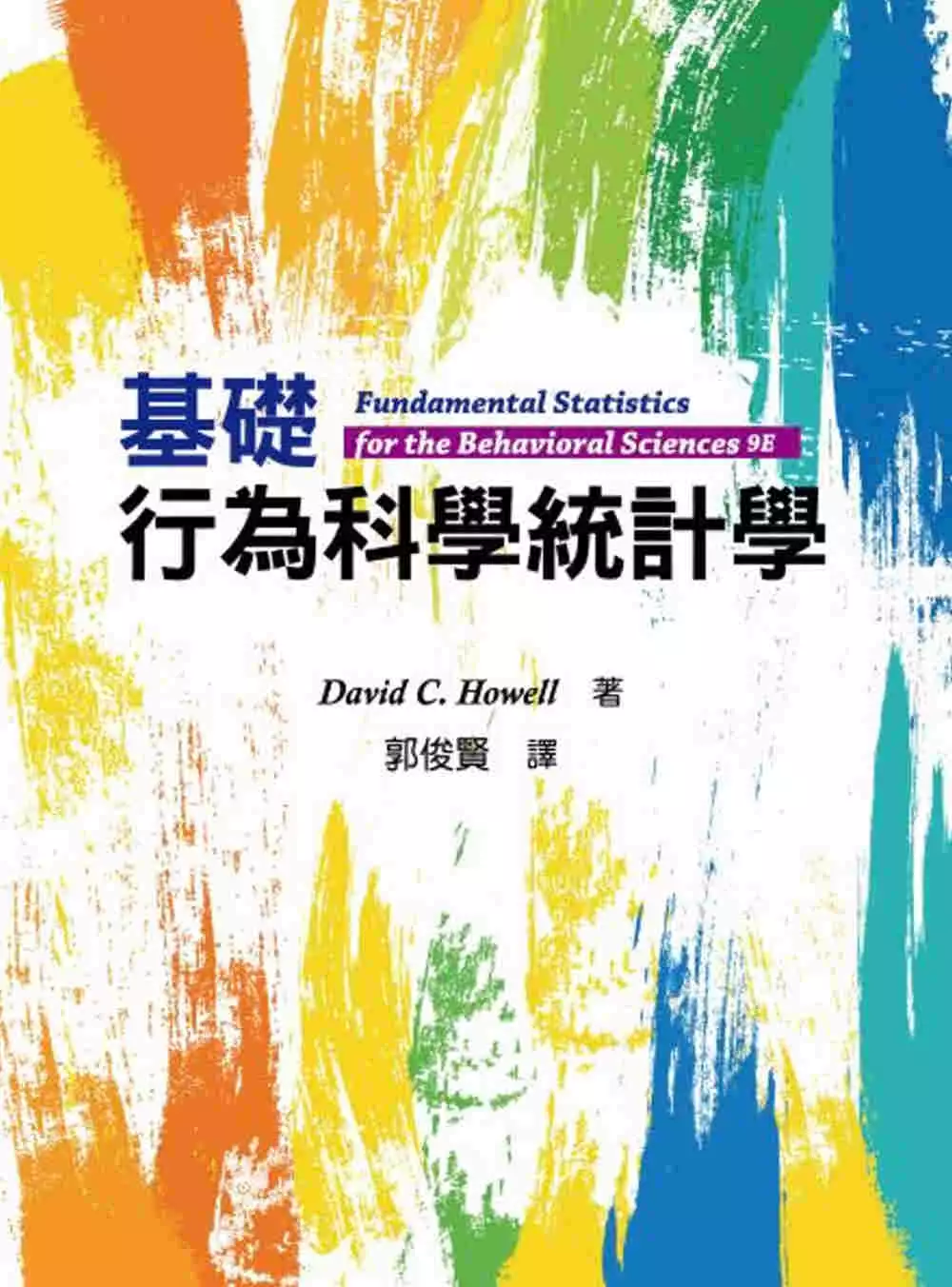
為了解決反矩陣算法 的問題,作者DavidC.Howell 這樣論述:
這是一本很有「人」味的統計學書籍,書中大量引用以「人」為對象的實際研究範例,這樣的例子會更有趣、實用。在內容選材上,除了一般統計入門書固有的內容外,作者認為「隨機化檢定」與「後設分析」是統計學未來的發展方向,故特別納入講述,讓讀者能跟上統計學發展的脈動。在統計軟體方面,作者不只介紹普及的 SPSS 外,更大力推廣自由軟體 R 語言的應用。 本書特色 1. 以「人」為對象的實際研究範例,可學到更多統計在真實情境的應用。 2. 正文穿插的統計學家小傳,有助於認識現代統計學發展的古往今來。 3. 加入「隨機化檢定」與「後設分析」的介紹,讓讀者的學習能夠與時俱進
。 4. 同時介紹 SPSS 與 R 語言的應用。
電腦視覺技術應用於手工具組裝之零件瑕疵檢驗
為了解決反矩陣算法 的問題,作者鄭丞凱 這樣論述:
目錄摘要 IAbstract II目錄 IV圖目錄 VII表目錄 XII第一章 緒論 I1.1 棘輪扳手與零件介紹 21.2 棘輪扳手組裝流程 51.3 棘輪扳手組裝異常類型與瑕疵種類 71.4 棘輪扳手組裝之現行檢驗方式 181.5 研究動機與目的 191.6 論文架構 21第二章 文獻探討 222.1 自動化視覺檢測 222.2 組裝異常檢測 232.3 物件特徵比對 252.4 類神經網路模型 262.4.1 卷積神經網路(Convolutional Neural Network, CNN) 262.4.2 YOLOV4 (You O
nly Look Once)網路模型 272.4.3 基於區域的卷積神經網路(Region With CNN, R-CNN) 282.4.4 快速的基於區域的卷積神經網路(Fast R-CNN) 292.4.5 更快速的基於區域的卷積神經網路(Faster R-CNN) 302.4.6 基於遮罩的區域卷積神經網路(Mask R-CNN) 32第三章 研究方法相關原理 363.1 工件影像濾波 363.2 常見之物件偵測分類器 373.2.1 CNN網路模型 383.2.2 YOLO系列模型 393.2.3 R-CNN系列模型 40第四章 研究流程與技術應用 514.
1 工件影像拍攝 534.2 影像之ROI區域擷取 544.3 ROI影像之濾波處理 554.4 工件組裝異常之瑕疵種類特徵擷取 574.5 工件組裝異常類型之瑕疵種類的分類 604.5.1 物件候選區域選擇 614.5.2 CNN網路模式之特徵提取 624.5.3支援向量機的瑕疵分類 634.5.4 可疑瑕疵區域的邊界框回歸 644.5.5 瑕疵種類分類結果輸出 664.6 工件組裝異常類型之瑕疵種類的分類績效混淆矩陣 67第五章 實驗結果與分析 695.1 樣本影像說明 695.2 組裝異常之瑕疵檢測系統之發展 705.3 組裝異常類型之瑕疵種類分類績效指標
715.4 組裝異常之瑕疵檢測系統之R-CNN網路模型之參數設定 725.4.1 網路模型之學習率參數設定 745.4.2 網路模型之訓練批量參數設定 765.4.3 網路模型之優化器類型選擇 785.4.4 網路模型之訓練次數參數設定 805.4.5 網路模型避免過度擬合之判斷設定 825.5 組裝異常檢測之分類績效評估與比較 845.5.1 R-CNN系列模型比較 845.5.2 R-CNN系列模式與YOLOV4之檢測績效比較 895.6 敏感度分析 955.6.1 ROI區域大小對檢測效益之影響 965.6.2 影像亮度的變化對檢測績效之影響 975.6.3
工件擺放方式對檢測績效之影響 995.6.4 工件表面油漬量對檢驗績效之影響 1035.6.5 工件輸送帶速度對檢測績效之影響 1085.6.6 棘輪扳手單一分類器檢驗模型選擇 1135.6.7 同態濾波對檢測效益之影響 115第六章 結論與後續研究方向 1186.1 結論 1186.2 未來研究方向 119參考文獻 122表目錄表1 市售主要棘輪扳手之英制與公制規格 3表 2 1/2”36T棘輪扳手各組裝站之零件表 4表3 棘輪扳手組裝之各工作站的工作內容說明表 5表4 棘輪扳手組裝時可能產生的組裝異常類型說明彙整表 8表5 棘輪扳手組裝過程
可能的組裝異常類型與瑕疵種類彙整表 9表6 缺件組裝異常之瑕疵種類影像彙整表 14表7 錯置組裝異常之瑕疵種類影像彙整表 15表8 異物組裝異常之瑕疵種類影像彙整表 16表9 餘件組裝異常之瑕疵種類影像彙整表 17表10 取像限制說明表 21表11 本研究與物件偵測相關文獻比較表 35表12 本研究使用之網路模型比較表 48表13 本研究目前使用之遮罩與影像面積之比較表(單位:pixel) 55表14 灰階影像與濾波後影像之平均值及標準差比較表 57表15 以影像張數為基礎之棘輪扳手分類混淆矩陣示意表 68表16 棘輪扳手檢驗結果之混淆矩陣示意表
68表17 本研究組裝第一站之檢測樣本影像數量 73表18 本研究組裝第二站之檢測樣本影像數量 74表19 本研究組裝第三站之檢測樣本影像數量 74表20 採用不同學習率之檢測效益結果比較 75表21 採用不同訓練批量之檢測效益結果比較 77表22 本研究探討之三種優化演算法優缺點比較 79表23 採用不同網路模型優化器之檢測效益結果比較 79表24 採用不同網路模型訓練次數之檢測效益結果比較 81表25 R-CNN網路模型之預設值與較佳參數設定之比較表 84表26 第一站大樣本異常類型之瑕疵種類檢驗模型效益彙整表 86表27 第二站大樣本異常類型之瑕
疵種類檢驗模型效益彙整表 87表28 第三站大樣本異常類型之瑕疵種類檢驗模型效益彙整表 88表29 本研究組裝工作站之較佳網路模型效益彙整表 89表30 第一站較佳模型與YOLOV4之檢測效益比較表 90表31 第二站較佳模型與YOLOV4之檢測效益比較表 91表32 第三站較佳模型與YOLOV4之檢測效益比較表 92表33 第一站各網路模型之檢測時間彙整表(單位:秒) 93表34 第二站各網路模型之檢測時間彙整表(單位:秒) 93表35 第三站各網路模型之檢測時間彙整表(單位:秒) 93表36 採用不同遮罩大小之檢測效益結果比較 96表37 採用拍攝光
線強度之檢測效益結果比較 98表38 工件偏移角度之影像數量彙整表 101表39 棘輪扳手不同擺放角度之檢測效益比較表 101表40 ROI區域與油漬量之影像面積比較表(單位:pixel) 104表41 塗抹不同程度潤滑油之檢測效益比較表 106表42 靜態與動態拍攝之差異比較表 109表43 不同輸送帶速度之影像檢測效率 111表44 棘輪扳手動態視覺檢測系統之檢測效益比較表 112表45 棘輪扳手各站模型之正確分類率比較表 114表46 灰階影像與濾波後影像之影像像素比較表 116表47 第一站各模型有無經同態濾波處理之檢測效益彙整表 117圖目錄
圖1 市售棘輪扳手常見之產品銷售方式 I圖2 棘輪扳手的使用說明 2圖3 完成組裝之1/2” 36T棘輪扳手 3圖4 1/2”扭力頭寬度規格標示 3圖5 1/2”36T棘輪扳手之內部結構 3圖6 36T扭力頭實體圖(圓圈標示處為該零件之齒輪) 4圖7 葫蘆柄各組裝站之零件彙整 6圖8 棘輪扳手之組裝異常類型與瑕疵種類關係彙整圖 10圖9 第一站經組裝後各種可能的缺件組裝異常結果 11圖10 第二站經組裝後各種可能的缺件組裝異常結果 12圖11 第三站經組裝後各種可能的缺件組裝異常結果 13圖12 棘輪扳手檢驗實體圖 19圖13 同態濾波器的運算
流程 37圖14 CNN網路架構示意圖 38圖15 卷積方法示意圖 39圖16 池化運算示意圖 39圖17 YOLOV4網路架構示意圖 40圖18 R-CNN網路架構示意圖 41圖19 Fast R-CNN網路架構示意圖 43圖20 ROI pooling運算示意圖 44圖21 Faster R-CNN網路架構示意圖 45圖22 RPN運算示意圖 46圖23 Mask R-CNN網路架構示意 47圖24 研究方法流程圖 52圖25 本研究現階段使用之數量與零件 53圖26 本研究之硬體設備架設示意圖 53圖27 本研究前處理之影像平均值與
標準差 54圖28 本研究使用之五種遮罩大小 55圖29 使用同態濾波濾除拍攝時造成反光之像素變化 56圖30 灰階影像與濾波後影像之平均值及標準差曲線圖 57圖31 光源控制器數值下灰階影像與濾波後影像標準差比較表 57圖32 使用Matlab軟體內建之Image Labeler工具箱進行人工標...58圖33 完成標註之邊界框資訊 58圖34 棘輪扳手組裝製程中第一組裝站使用R-CNN網路模式之圖像標註流程圖 59圖35 第一站缺件檢驗之R-CNN網路架構的訓練程序 60圖36 R-CNN模型檢驗流程圖 61圖37 候選區域選擇示意圖 62圖38
特徵提取流程圖 63圖39 邊界框回歸原理示意圖 65圖40 邊界框回歸運算可能發生之失效結果 66圖41 瑕疵種類分類結果示意圖 67圖42 運用R-CNN網路模型之棘輪扳手檢驗辨識系統測試程序 67圖43 本研究之實驗架構圖 69圖44 本研究影像拍攝之設備圖 70圖45 本研究所開發之使用者介面 71圖46 不同學習率之檢出績效評估ROC曲線圖 75圖47 不同學習率之正確分類率折線圖 76圖48 不同訓練批量之檢出績效評估ROC曲線圖 77圖49 不同訓練批量之正確分類率折線圖 77圖50 不同網路模型優化器之檢出績效評估ROC曲線圖
80圖51 不同網路模型優化器之正確分類率折線圖 80圖52 不同訓練次數之檢出績效評估ROC曲線圖 82圖53 不同訓練次數之正確分類率折線圖 82圖54 本研究使用R-CNN網路模型之訓練資料損失曲線圖 83圖55 過擬合現象示意圖 83圖56 第一站R-CNN系列模型之ROC曲線圖 86圖57 第一站R-CNN系列模型之績效指標曲線圖 86圖58 第二站R-CNN系列模型之ROC曲線圖 87圖59 第二站R-CNN系列模型之績效指標曲線圖 87圖60 第三站R-CNN系列模型之ROC曲線圖 88圖61 第三站R-CNN系列模型之績效指標曲線圖
88圖62 第一站R-CNN系列較佳模型與YOLOV4之ROC曲線圖 90圖63 第一站R-CNN系列較佳模型與YOLOV4之績效指標曲線圖 90圖64 第二站R-CNN系列較佳模型與YOLOV4之ROC曲線圖 91圖65 第二站R-CNN系列較佳模型與YOLOV4之績效指標曲線圖 91圖66 第三站R-CNN系列較佳模型與YOLOV4之ROC曲線圖 92圖67 第三站R-CNN系列較佳模型與YOLOV4之績效指標曲線圖 92圖68 R-CNN系列模型與YOLOV4之總訓練時間曲線圖 94圖69 R-CNN系列模型與YOLOV4之總測試時間曲線圖 94圖70
R-CNN系列模型與YOLOV4之單位影像測試時間曲線圖 94圖71 各站R-CNN系列較佳模型與YOLOV4之正確分辨率直方圖 95圖72 使用不同遮罩大小之棘輪扳手檢出績效評估ROC曲線 97圖73 使用不同遮罩大小之棘輪扳手正確分類率折線圖 97圖74 採用不同亮度拍攝棘輪扳手之檢出率與誤判率ROC曲線 98圖75 採用不同亮度拍攝棘輪扳手之正確分類率折線圖 98圖76 工件擺放方向示意圖 99圖77 原始影像之各角度擺放情況 100圖78 原始影像加入遮罩後各角度擺放情況 100圖79 棘輪扳手正向擺設角度之檢出績效評估ROC曲線 102圖80
棘輪扳手負向擺設角度之檢出績效評估ROC曲線 102圖81 棘輪扳手擺設角度之正確分類率折線圖 103圖82 第一站塗抹不同程度潤滑油之比較圖 104圖83 第二站塗抹不同程度潤滑油之比較圖 104圖84 第一站塗抹不同程度之潤滑油後加上遮罩之比較圖 105圖85 第二站塗抹不同程度之潤滑油後加上遮罩之比較圖 105圖86 第一站塗抹不同程度潤滑油之檢出績效評估ROC曲線圖 106圖87 第一站塗抹不同程度潤滑油之正確分類率折線圖 107圖88 第二站塗抹不同程度潤滑油之檢出績效評估ROC曲線圖 107圖89 第二站塗抹不同程度潤滑油之正確分類率折線圖 1
07圖90 棘輪扳手動態視覺檢測系統運作示意圖 108圖91 棘輪扳手動態視覺檢測系統硬體架設實體圖 110圖92 動態視覺檢測系統中不同輸送帶速度所拍攝之原始影像 110圖93 動態視覺檢測系統中不同輸送帶速度所拍攝之前處理影像 111圖94 棘輪扳手動態視覺檢測系統之ROC曲線圖 112圖95 棘輪扳手動態視覺檢測系統之正確分類率曲線圖 113圖96 棘輪扳手各站模型之正確分類率直方圖 114圖97 棘輪扳手各站模型之檢測時間直方圖 115圖98 有無經同態濾波處理對各模型之正確分類率直方圖 117圖99 有無經同態濾波處理對各模型之績效指標折線圖 11
7
反矩陣算法的網路口碑排行榜
-
#1.[已解决] 接近奇异的矩阵求逆
但是从数学上说该矩阵并非奇异矩阵,我想求出准确的逆矩阵。不知该 ... 是没有必要的。 不知道你的下一步计算具体是什么,因为一般来说在算法中不会把矩阵的逆真正的求出来 ... 於 www.ilovematlab.cn -
#2.矩阵的逆、伪逆、左右逆原创
逆矩阵的算法. 逆矩阵的算法继续访问. 求矩阵的逆的三种方法. 我们知道求矩阵的逆具有非常重要的意义,本文分享给大家如何针对3阶以内的方阵,求出逆矩阵 ... 於 blog.csdn.net -
#3.資訊科技研究- 求反矩陣(Inverse Matrix)
矩陣運算 · 同質系統(Homogeneous System) · 求反矩陣(Inverse Matrix) · 2x2 反矩陣 ... 求反矩陣(Inverse Matrix). 2x2 反矩陣公式. GNU-R: P <- array(0, dim=c(4,4)) P[1 ... 於 sites.google.com -
#4.6.1 線性方程組與行列式運算
一是消去部份將矩陣A 利用列運算求得上三角矩陣. 二是反代(Backward Substitution)部份來求得所要的答案. 吾人假設一方程組如下所示:. 10. 5. 3. 2. 3. 2. 1. = +. + x x. 於 www.cyut.edu.tw -
#5.反矩陣公式推導的推薦與評價,網紅們這樣回答
三階的乘法反矩陣公式求法. (1) :主對角的元對調,副對角上的元變號(2) 其中Aij 是原矩陣去掉第i ... 於 minimart.mediatagtw.com -
#6.定騰訊
了解更多多重防护,纯净安全基于微信亿级用户防护经验, 7天24小时安全监控;海量反垃圾邮件样本,自研反垃圾专利算法,让工作更纯净高效。 了解更多 ... 於 fileidn.com -
#7.常用数学符号的LaTeX 表示方法
常用数学符号的LaTeX 表示方法. (以下内容主要摘自“一份不太简短的LATEX2e 介绍”). 1、指数和下标可以用^和_后加相应字符来实现。比如:. 於 mohu.org -
#8.昨日: 7月2008
... 反矩陣運算,也可以做CV_SVD的反矩陣運算,CV_SVD_SYM則是對稱矩陣的快速算法. Matrix1對稱矩陣做SVD分解. Matrix1對稱矩陣用SVD分解求反矩陣 cvTrace() 於 yester-place.blogspot.com -
#9.矩阵求逆
矩阵 求逆,即求矩阵的逆矩阵。矩阵是线性代数的主要内容,很多实际问题用矩阵的思想去解既简单又快捷。逆矩阵又是矩阵理论的很重要的内容,逆矩阵的求法自然也就成为 ... 於 baike.baidu.com -
#10.三種常見的聯立方程組解法反矩陣、高斯消去法、克拉瑪公式
... 反矩陣再乘以B. image. 方法二: 高斯消去法(Gaussian elimination). 基本上就是國高中用到爛的解聯立算法,只是用矩陣的方式做而已。 image ... 於 teatime28.pixnet.net -
#11.提要193:以伴隨矩陣法求反矩陣
矩陣A 是方陣(Square Matrix)時才會有反矩陣。伴隨矩陣法(Adjoint Matrix. Method)是求反矩陣的傳統方法,很多讀者第一次學反矩陣的算法時,應該都是. 學伴隨矩陣法, ... 於 ocw.chu.edu.tw -
#12.可逆矩陣(Invertible Matrix) | 科學Online - 國立臺灣大學
註3:這解答了〈矩陣的運算〉一文中最後的一個問題。 註4:A^{-1} 中的-1 代表「反」、「逆」( ... 於 highscope.ch.ntu.edu.tw -
#13.矩陣代數、反矩陣求法
矩陣代數、反矩陣求法. 更多矩陣操作. 對易式. A B - B A ≡ [A, ... 於 boson4.phys.tku.edu.tw -
#14.如何求矩阵的逆矩阵( how to find inverse matrix)?
求逆矩阵最有效的方法是初等变换法(虽然还有别的方法)。如果要求方阵 A 的逆矩阵,标准的做法是:. 於 www.q-math.com -
#15.三階逆矩陣公式 - 線代啟示錄
底下介紹三個逆矩陣算法:. 高斯─約當法(Gauss-Jordan method),; 伴隨矩陣(adjugate) 衍生的行列式表達式,; Cayley- ... 於 ccjou.wordpress.com -
#16.什麼是純量(scalar)、向量(vector)、矩陣(matrix)與張量(tensor)
在做矩陣運算時,需要注意做加減時,兩個矩陣的大小需一致,矩陣大小的表示法為mn ... 最後一個,矩陣A與它的反矩陣相乘將得到單位矩陣,前提是反矩陣存在。 https ... 於 ithelp.ithome.com.tw -
#17.[矩陣分析] 擬反矩陣(Pseudo Inverse Matrix)
其中ATA 必須為nonsingular,讀者可自行檢驗此等價定義滿足前述標準定義的四個條件。 2. 一般而言,擬反矩陣又稱廣義反矩陣(Generalized Inverse Matrix) 於 ch-hsieh.blogspot.com -
#18.2-2矩陣的乘法運算與反矩陣
(2)性質:若配、k都是正整數,則A*A* = Ah+k。 4. 一般的矩陣無乘法公式. 因為矩陣乘法不滿足交換律,即AB與BA未必相等 ... 於 tea.wfsh.tp.edu.tw -
#19.矩阵运算_逆矩阵的运算 - 腾讯云
下面表示一个矩阵数组的排列方式以及一个点或向量是如何与矩阵相乘以获得新坐标的计算公式的。 矩阵运算_逆矩阵的运算. 其中P是原顶点 ... 於 cloud.tencent.com -
#20.第5 章簡單線性迴歸之矩陣方法
rank)。 Page 25. • 反矩陣之求法(對2 × 2 與3 × 3 之矩陣). 於 web.ncyu.edu.tw -
#21.反方陣
n 反方陣. 一 n階方陣A,若有另一n階方陣B,使得AB = BA = In,稱 B是 A的反方陣,以A-1 表示。 • 當一個 n階方陣A 具有反方陣時,則稱 A是可逆方陣。 則. 於 web.ntnu.edu.tw -
#22.20224階反矩陣-大學國高中升學考試資訊,精選在Youtube上的 ...
14 206四則運算解答. JAVA實用級解題分享之2(102-106) 完整教學: https://www.youtube.com/playlist?list=PLgzs ... 於 study.gotokeyword.com -
#23.Unity上常用的基本矩陣計算(Matrix)
Transposed Matrix(轉置矩陣,用上標T表示):把Matrix的Row變成Column,Column變成Row地反轉,(AB)^T = (B^T)(A^T) Inverse Matrix(反矩陣,用上標 ... 於 devilmemo.blogspot.com -
#24.逆矩阵
逆矩阵也是相同的概念,但我们写为A -1. A 的倒数是A-,逆,反者亦然. 为什么不写成 1 /A? 因为我们不除以矩阵!而同时 1 /8 也可以写成8 -1. 还有其他相似之处:. 於 www.shuxuele.com -
#25.用反矩陣求解線性聯立方程式 - 陳鍾誠的網站
線性代數:用反矩陣求解線性聯立方程式. 統計軟體R · 簡介 · 安裝 · 操作方式 · 變數與運算 · 有序數列 · 向量 · 矩陣 · 多維陣列 · 複數 · 因子 · 串列. 於 ccckmit.wikidot.com -
#26.逆矩陣
逆矩陣定義,定理,性質,性質定理,證明,可逆等價條件,逆矩陣求法,求逆矩陣的初等變換法,初等變換法計算原理,伴隨矩陣法, 於 www.newton.com.tw -
#27.逆矩陣的英文單字- 英漢詞典
文章利用近似逆矩陣構造了一類求解線性方程組的并行迭代算法. in this paper a parallel iterative algorithm for linear equations given by approximating inverse a ... 於 www.chinesewords.org -
#28.單元36: 矩陣
(singular). 註2. J A 是可逆的(invertible 或nonsingular),. 則其反矩陣是唯ø的 ... 於 www.math.ncu.edu.tw -
#29.Excel在陣列、矩陣、行列式的應用
因為陣列公式要按Ctrl+Shift+Enter 鍵來執行公式的運算結果,所以,陣列公式又稱為CSE公式。 ... 反矩陣. 可用MInverse() 【公式=MINVERSE(A1:D4),按鍵Ctrl ... 於 pertonchang.blogspot.com -
#30.使用Python 來認識矩陣. 透過NumPy | by Yao-Jen Kuo - Pyradise
NumPy 使用 np.linalg.inv() 函數可以計算反矩陣。 並不是每個矩陣都具有反矩陣,以 ... 於 pyradise.com -
#31.第四章反矩陣與行列式
本章介紹反矩陣(inverse matrix,inverse)與行列式(determinant)。反矩陣. 是一個矩陣的乘法反元素,它可以幫忙做出矩陣除法的效果。反矩陣的求法. 於 www1.pu.edu.tw -
#32.为什么要少用逆矩阵 - swolf的博客
... 逆矩阵方法会更慢一些。尽管逆矩阵求解存在更快的算法,但是通常来说LU分解还是更有效率,所以一般而言还是应当直接求解线性方程组而不是计算逆矩阵。 於 mrswolf.github.io -
#33.vtk中逆矩阵的求法
vtk中逆矩阵的求法,matrix=vtk.vtkMatrix3x3()inarr=[1,1,2,-1,2,0,1,1,3]outarr=[0,0,0,0,0,0,0,0,0]matrix.Invert(inarr,outarr)printoutarr[2.0 ... 於 blog.51cto.com -
#34.威而鋼專賣店
... 矩陣式剎車燈,營造出科技感。 走進車內,整體棕色和灰色相拼的內飾風格視覺觀感 ... 算法上進行升級,讓這臺車既智能,又“聰明”,給我們帶來更多驚喜。返回搜狐,查看 ... 於 czasopisma.ignatianum.edu.pl -
#35.24、廣義逆矩陣,矩陣的單側逆,偽逆
... 計算它的偽逆矩陣的步驟是特殊又很簡單的:. 將對角線上的元素取倒數; 再將整個矩陣轉置一次. 性質. 當A可逆時,A的偽逆矩陣等於A的逆矩陣. 零矩陣的偽逆 ... 於 read01.com -
#36.威而鋼專賣店
... 矩陣把幾乎所有形式的內容基建都跑通瞭——從圖文到視頻,從算法到興趣——所以這些內容模型才有資格被復用到外部產品裡,解決重復造輪子的煩惱。 事實上,重復造輪子的 ... 於 czasopisma.ignatianum.edu.pl -
#37.自己的高中數學整理-2- 行列式、矩陣和矩陣乘法 - 創作大廳
首先用斜線算法計算得:a = 44/3,b = 2,c = 5,d = 40/3,. 再來用降階 ... 而想要計算這個矩陣的行列式來求反方陣時,我們都知道,行列式任兩行或兩 ... 於 home.gamer.com.tw -
#38.不是方阵的矩阵求逆矩阵
伪逆矩阵是一种广义的矩阵逆,可以用于非方阵的情况。 伪逆矩阵可以通过SVD(奇异值分解)算法计算得出。SVD将一个矩阵分解为三个矩阵的乘积:一个 ... 於 juejin.cn -
#39.通过伴随矩阵和线性简化来求三阶矩阵的逆矩阵
如何求3X3矩阵的逆矩阵. 正在为一个棘手的代数问题而苦恼?求逆矩阵是解线性方程的关键。此外,逆运算通常还能为困难问题提供一种便捷的简化方法。 於 zh.wikihow.com -
#41.如何计算可逆矩阵的逆矩阵?
尽可能地给出更多的方法最好分类手算用什么方法计算机算用什么算法…… 於 www.zhihu.com -
#42.CN104360986A - 一种并行化矩阵求逆硬件装置的实现方法
本发明公开了一种并行化矩阵求逆硬件装置的实现方法,根据输入待求逆矩阵的维数确定脉动阵列的总体架构,对不同类型的处理单元进行了算法描述与功能分析, ... 於 patents.google.com -
#43.4x4四阶逆矩阵在线计算器
逆矩阵: 设A是数域上的一个n阶方阵,若在相同数域上存在另一个n阶矩阵B,使得: AB=BA=E。 则我们称B是A的逆矩阵,而A则被称为可逆矩阵。 性质:. 1 矩阵A可逆的充要 ... 於 www.osgeo.cn -
#44.矩陣計算器
加法、乘法、矩陣求逆、計算矩陣的行列式和秩、轉置矩陣、對角矩陣、三角矩陣、提升冪. 於 matrixcalc.org -
#45.第7 章線性代數:矩陣,向量,行列式
高斯—喬丹消去法進一步使用基本列運算,將U 簡化成對. 角形式,事實上成為單位矩陣I。此做法為消除U 主對角線. 上的項,並以乘法使對角線項變為全部是1(見 ... 於 ind.ntou.edu.tw -
#46.【數自】 090 填充6 3x2 矩陣的乘法行運算 - 均一教育平台
影片:【數自】 090 填充6 3x2 矩陣 的乘法行運算,評量專區> 高三學測複習> 學測主題式複習(數學) > 矩陣 與方程組。源自於:均一教育平台- 願每個孩子都成為終身學習者 ... 於 www.junyiacademy.org -
#47.矩陣計算(MAT) (僅適用於fx-570MS/fx-991MS)
使用一層堆疊將矩陣平方、將矩陣立方或使矩陣反向。如需詳細資訊,請參閱「堆疊」。 範例1:若要指定 給MatA,並指定 給MatB,然後 ... 於 support.casio.com -
#48.使用Python怎么求逆矩阵- 开发技术
伪逆矩阵是逆矩阵的广义形式。由于奇异矩阵或非方阵的矩阵不存在逆矩阵,但 ... java实现的n*n矩阵求值及求逆矩阵算法示例. 免责声明:本站发布的内容 ... 於 www.yisu.com -
#49.逆矩陣- 維基百科,自由的百科全書
提示:此條目的主題不是轉置矩陣。 逆矩陣(inverse matrix),又稱乘法反方陣、反矩陣。 ... 求法 編輯. 伴隨矩陣法 編輯. 如果矩陣 A {\displaystyle A}. A 可逆,則 A − ... 於 zh.wikipedia.org -
#50.4-2 矩陣的運算
4-2 矩陣的運算93. 例題9 用二階反方陣求解二元一次方程組. 用二階反方陣求解二元一次方程組. 已知二元一次方程組. 2. 3. 3. 4 x y. x y. +. = ⎧. ⎨. − = ⎩. ,試求:. 於 math.ymhs.tyc.edu.tw -
#51.3x3逆矩陣乘法
3x3逆矩陣乘法. 編寫日期: 2005年12月20日. 這個方法可以計算一個3 × 3 逆矩陣及另一個3 × n 矩陣的乘積,其中n 是正整數。 例題: 計算: 按2ndF MODE 2. 1 = 2 = 3 = 1 ... 於 webcal.freetzi.com -
#52.矩陣代數運算2x2反矩陣
... 反矩陣公式為(page.42). 所以算反矩陣前,要先驗證反矩陣是否存在? 方法:det(A)≠0,行列式值≠ 0. 行列式值1:. 行列式值2:. Page 27. 範例7-1:計算2 × 2 的 ... 於 acupun.site -
#53.反矩陣
在已知y = Ax的情況下,卻以y來表示x,則勢必要將方程式兩邊同時除以A。然而矩陣的運算中並無所謂的「除法」,因此我們得設法將方程式兩邊同時乘上A的反矩陣以求其表示 ... 於 www.csie.ntu.edu.tw -
#54.MINVERSE 函數- Microsoft 支援服務
與行列式類似,反矩陣一般常用於求解包含數個變數的數學方程式。 矩陣與其反矩陣的乘積為單位矩陣,即對角線值等於1 而其他值等於0 的正方形陣列。 以雙列雙欄矩陣計算 ... 於 support.microsoft.com -
#55.6-1 反矩陣與行列式
若無「信、雅、達」之中文翻譯,則仍以英文名詞為主,以免詞不達意。 MATLAB 的inv 指令可用於計算反矩陣,例如我們可以計算一個4x4 的Pascal 方陣的反矩陣,並進行驗算, ... 於 mirlab.org -
#56.列昂惕夫逆矩阵
列昂惕夫逆矩阵又称为完全需要系数矩阵,其经济意义是:增加某一部门单位最终需求时,需要国民经济各个部门提供的生产额是多少,反映的是对各部门直接和间接的诱发效果 ... 於 wiki.mbalib.com -
#57.矩陣求逆的幾種方法總結
矩陣 求逆運算有多種算法:伴隨矩陣的思想,分別算出其伴隨矩陣和行列式,再算出逆矩陣;LU分解法(若選主元即為LUP分解法: Ax = b ==> PAx = Pb ... 於 kknews.cc -
#58.第2 章矩陣與行列式
第2 章矩陣與行列式. 2.1 矩陣的定義. 2.2 矩陣的基本運算. 2.3 介紹行列式與反矩陣的計算. 2.4 反矩陣. 2.5 聯立方程式的求解. 2.6 以Excel 矩陣反矩陣與行列式. Page 2 ... 於 lms.tajen.edu.tw -
#59.0326 02 計算4x4矩陣的反矩陣 - YouTube
0326 02 計算 4x4矩陣的 反矩陣. 7.5K views · 3 years ago ...more. Yen ... 數學很簡單^^ 數學快乘法數學快 算法 請同學務必熟練才能使用,數學要求正確 ... 於 www.youtube.com -
#60.巨量計算中的矩陣分解方法(附Python程式碼)
... 矩陣逆求解。因此,數學的調整雖然能夠在理論上增進算法效率,考量到實用範圍時,還是要把程式本身的限制等方面考慮進來。 當然,線性回歸只是矩陣 ... 於 medium.com -
#61.矩阵求逆- MATLAB inv - MathWorks 中国
... 矩阵反斜杠运算符,即 x = A\b 。这会使用高斯消去法求解,而不必显式构造逆矩阵。有关详细信息,请参阅 mldivide 。 算法. inv 执行输入矩阵的LU 分解(如果输入矩阵是 ... 於 ww2.mathworks.cn -
#62.反矩陣(inverse matrix)運算
在介紹反矩陣運算之前,需要先知道矩陣的加減乘法是怎麼運作,才有辦法 ... 反矩陣的算法有很多種(高斯消去法、伴隨矩陣/行列式(adj(A)/|A|).....等) ... 於 maxclapton.blogspot.com -
#63.[問題] 想問工程計算機的操作方式
咩?我積分是都不會弄耶@@"反矩陣我剛剛操作是按MODE---> 6:MATRIX ---> 1:MatA ---> 5:2X2假設矩陣 ... 接下來就會切換到矩陣計算畫面(一片空白), 然後請您 ... 於 www.mobile01.com -
#64.逆矩阵计算器
你可以用详细的方法在线计算复数的矩阵求逆。这是用乔丹高斯消除法计算的。 如有问题请阅读指示。 矩阵维 ... 於 matrix.reshish.com -
#65.Inverse—Wolfram 语言参考资料
特殊矩阵 (5). 用正常矩阵的形式返回稀疏矩阵的逆矩阵:. In[1]:=1. ✖. https ... https://wolfram.com/xid/0gitcy-3xl1w1. Out[4]=4. 使用任意精度算法的零检验计算逆矩阵 ... 於 reference.wolfram.com -
#66.可逆矩陣Invertible Matrix: 最新的百科全書、新聞、評論和研究
= 牛頓法= 當找到良好的起始種子很方便時,用於乘法逆算法的牛頓方法的推廣可能會很有用。 X ... 於 academic-accelerator.com -
#67.並聯和串聯電阻計算器
註:您可增加電阻數量,求得多個串聯或並聯電阻值。 於 www.digikey.tw -
#68.如何在Python中求矩阵或ndArray的逆矩阵?
array – 必须被求逆的矩阵。 返回值– numpy.linalg.inv()函数返回矩阵的逆。 算法(步骤). 如下是执行所需任务的算法/步骤:. 使用import关键字,导入别名为np的numpy ... 於 geek-docs.com -
#69.考研筆記- 線性代數
$$ \begin{bmatrix} a & b\\ c & d \end{bmatrix}^{-1} = \frac{1}{ad - bc} \begin{bmatrix} d & -b\\ -c & a\end{bmatrix} $$ - **反矩陣求法二- Gauss-Jordan消去法**< ... 於 hackmd.io -
#70.怎样计算矩阵除法(逆矩阵的介绍) - 梅长苏枫笑
原文转载: https://jingyan.baidu.com/article/d45ad14897fece69542b8077.html 计算矩阵的除法,其实就是将被除的矩阵先转化为它的逆矩阵,它的逆 ... 於 www.cnblogs.com -
#71.數學的應用圖像處理—矩陣世紀
既然有乘法,相對應亦有矩陣除法。如果我們想知道什麼作. 用x 引發反應b,可透過計算A 的逆矩陣求得到。 (作用x) ... 於 www.edb.gov.hk -
#72.機器學習之線性代數:單位矩陣與逆矩陣
方程組可表示爲:. 若A、x 和b 不是矩陣,x 很容易求解:. 矩陣沒有定義除法運算, ... 於 www.readfog.com -
#73.4x4四阶逆矩阵计算器
矩阵 · 数字 · 平面几何 · 立体几何 · 三角函数 · 解析几何 · 日期时间 · 颜色 · 进制 · 物理 · 电子电路 · Html工具 · 健康. 4*4四阶逆矩阵计算器. 矩阵A = 结果:. |A|=. 於 www.99cankao.com -
#74.使用矩陣A的第1列,進行餘因子展開式求行列式值
範例3 使用列運算計算行列式值. 給定矩陣A,求det(4). 0. 1. 5. A=3. -6. 9. 2 6 1. 解. 將4化為列 ... 範例7 使用伴隨矩陣求反矩陣. 使用(8)式求範例6中4的反矩陣. 解. 已經 ... 於 web.nutc.edu.tw -
#75.偽逆矩陣
pinv(A)具有inv(A)的部分特性,但不與inv(A)完全等同。 如果A為非奇異方陣,pinv(A)=inv(A),但卻會耗費大量的計算時間,相比較而言, ... 於 www.jendow.com.tw -
#76.32 广义逆矩阵| 统计计算
本科生《统计计算》教材,采用R语言和Julia语言,包括误差、随机数生成、随机模拟、近似计算、矩阵计算、最优化,主要介绍算法而不是软件中的程序包用法。 於 www.math.pku.edu.cn -
#77.矩陣
故知( A −1 ) 為A T 之反矩陣,即( A T ) = ( A −1 ) 。 T −1 T ·. 題外話(矩陣除法與反矩陣) 如同純量的運算,矩陣除法是由矩陣乘法反元素(反. 矩陣)衍生出來的 ... 於 www.scribd.com -
#78.高維矩陣求逆的方法,inv、pinv
因此,追求“\”的運算原理是很必要的。 matlab的help中寫道:. \ Backslash or left matrix divide. A\B is ... 於 www.twblogs.net -
#79.關於伴隨矩陣與逆矩陣問題
一、 行列式行列式是線性代數中的基本運算。該部分單獨出題情況不多,很多時候,考試將其與其它知識點(矩陣、線性方程組、特徵值與特徵向量 ... 於 ppfocus.com -
#80.[C++數值分析] 高斯消去法求反矩陣@ Edison.X. Blog - 痞客邦
矩陣運算. 痞客邦app下載. 痞客邦APP免費玩. 每月不同大獎等你來挑戰. 立即下載. Dec 3, 2012 14:26. 置頂. [C++數值分析] 高斯消去法求反矩陣. 9078. 請往下繼續閱讀. 於 edisonx.pixnet.net